Warp thread feed to weaving machines
The warp thread tension has become one of the most important process variables of the weaving process. Too high and low warp thread tension leads to warp thread breaks, which counteract a good weaving behavior and efficiency.
For the economic production of fault-free woven fabrics, the warp threads have to be feed with an equal length and tension to the weaving machine.
It can be distinguished between various warp thread feeding methods for instance through feeding from warp beams inside the weaving machine, feeding from separate warp beams outside the weaving machine and feeding from creels.
Warp beams inside the weaving machine
Good warp preparation ensures properties for a great weaving machine efficiency. The high quality for clothing fabrics as well as technical fabrics requires a gentle warp thread feed from the warp beam to the web position.

CREALET: Warp Let-off on Projectile Weaving Machine
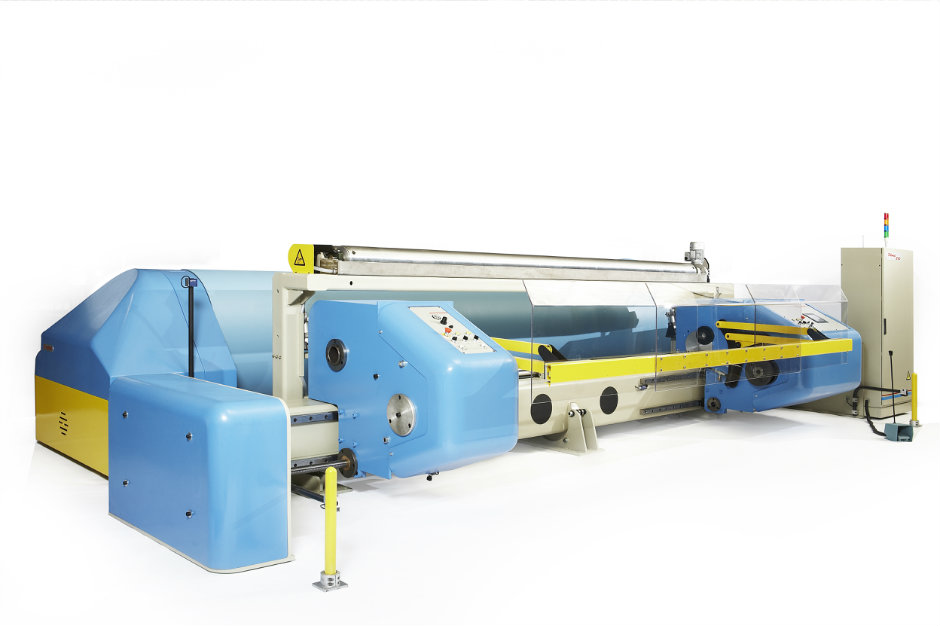
COMSAT: Sectional Warping Machine
As the world’s leading manufacturer of electronically controlled warp feed systems for wide and narrow weaving machines, we offer you innovative solutions.
In cooperation with our partner COMSAT, a leading company of Direct and Sectional Warpers, we can also present high-quality solutions in warp preparation to you.
Warp beams outside the weaving machine

Warp Beam Frame for Conveyor Belt
Warp beams outside the weaving machines are placed in separately standing warp beam frames. The requirements are extremely wide, ranging from weaving of very heavy conveyor belts to very sensitive rubber bands for underwear.
Warp beams can be specially designed for the use of large warp beams. This increases the warp capacity and reduces the number of warp beam changes.
On the other hand, warp beam frames are used for fabrics with different warp systems with different yarn counts or different weaves.
The warp beam infrastructures in narrow weaving are often equipped with small warp beams, which work with a simple rope brake and weight system.
The disadvantage of such friction brakes are yarn tension peaks caused by the breakaway torque when starting the weaving machine. Furthermore, an increasing warp tension is noted when the warp beam diameter gets smaller.
Benefit from our many years of experience and our technical know-how in all aspects of warp feeding.
Weaving from bobbin creel
Warp feeding from creels to weaving machines can be done in two different ways.
For tape yarn unrolling creels are in use for twist-free supply of the yarn to the weaving machine.
Wherever possible creels with over head draw-off can be used. The creel structure usually requires a large and roomy area behind the weaving machine.
Weaving from creels are done with tensioners, to equalize the warp tension of each individual warp thread. Moreover, for easy handling warp feeding systems are placed between creel and weaving machines.
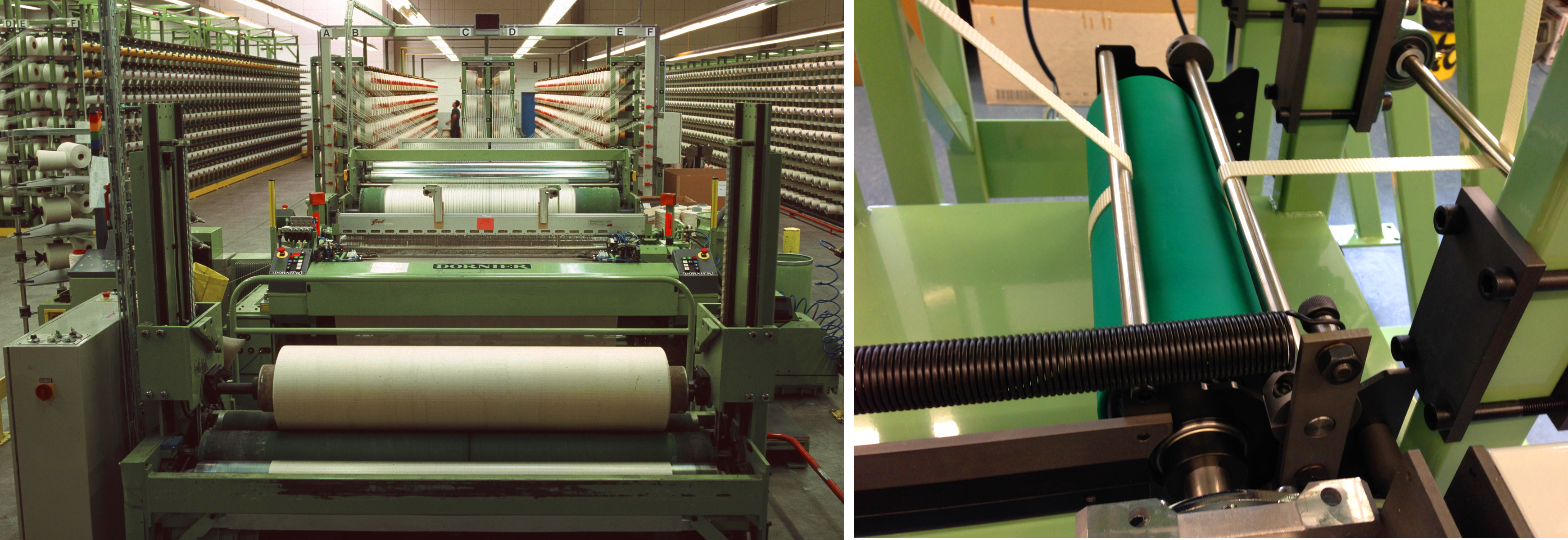
(l) Warp Feeding System with Unrolling Creel for Tire Cord Fabric / (r) Warp Feeding System for Narrow Webbings
Warp feeding systems between creel and weaving machines belong to our core competence. Together with our partners, we also offer creels for other, diverse areas of application.